Quality operations – your biggest threat or greatest asset?
Our regulatory landscape seems to produce new quality mandates and guidelines nearly every day, creating significant challenges for any quality professional. How can you ensure the highest levels of product safety and efficacy, while simultaneously moving product as quickly as possible through your supply chain to meet your increasingly crunched production schedule?
Solutions
With Clarkston as your partner, we design and implement quality processes and systems that fit your organizational objectives – today and tomorrow.
Sustainable and effective quality combines people, process, and technology; and begins with a base of learning and organizational design that nurtures both capability and culture.
- Organizational Effectiveness
- Training
- Harmonization
- Change Management
- Testing
- Validation
Realizing operational efficiencies in your quality management processes improves your ability to both deliver safe and effective products, and handle out-of-specification events.
- Annual Product Review
- Batch Release
- Packaging and Labeling
- Complaint Management
- Supplier Management
- Deviation Management/CAPA
Fully harmonized systems of data and technology are your greatest asset for continuous quality.
- Global Deployments of Quality Systems (e.g. TrackWise, Veeva, Labware, LabVantage)
- Systems and Data Integration Roadmap
- LIMS Implementation and Support
- eQMS Implementation and Support
- EDMS Implementation and Support
- Learning Management Systems (LMS) Implementation and Support
- Materials Management
What Our Clients Say
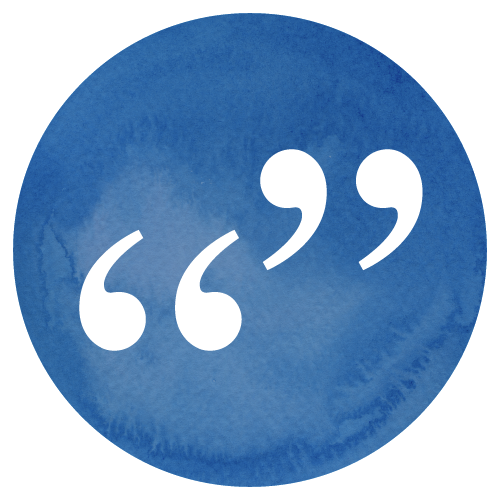
Director, Global Quality Operations
“Clarkston is proactive in bringing continuous improvement ideas to the table. I value the experience they provide in the LIMS space. I haven’t seen this level of experience with other professional service providers we’ve engaged with.”
Chief Technical Operations and Quality Officer
“My experience has been fantastic — great relationships, and everybody shows up incredibly professional. [Clarkston] really drives for results, so we don’t have to (so to speak). They really just have a way of being able to motivate the teams, energize the teams, and have fun along the way.”
We helped a life sciences manufacturer reduce lab cycle times by 60% and manufacturing cycle times from 120 days to 60 through assessment of their existing quality processes and implementation of new protocols and efficiencies. For more information on how we can help your company, please contact our quality operations expert, LaToya Lee Jones.
Clarkston's Quality System Experience
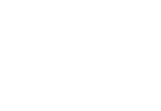

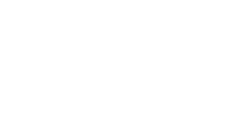
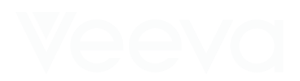